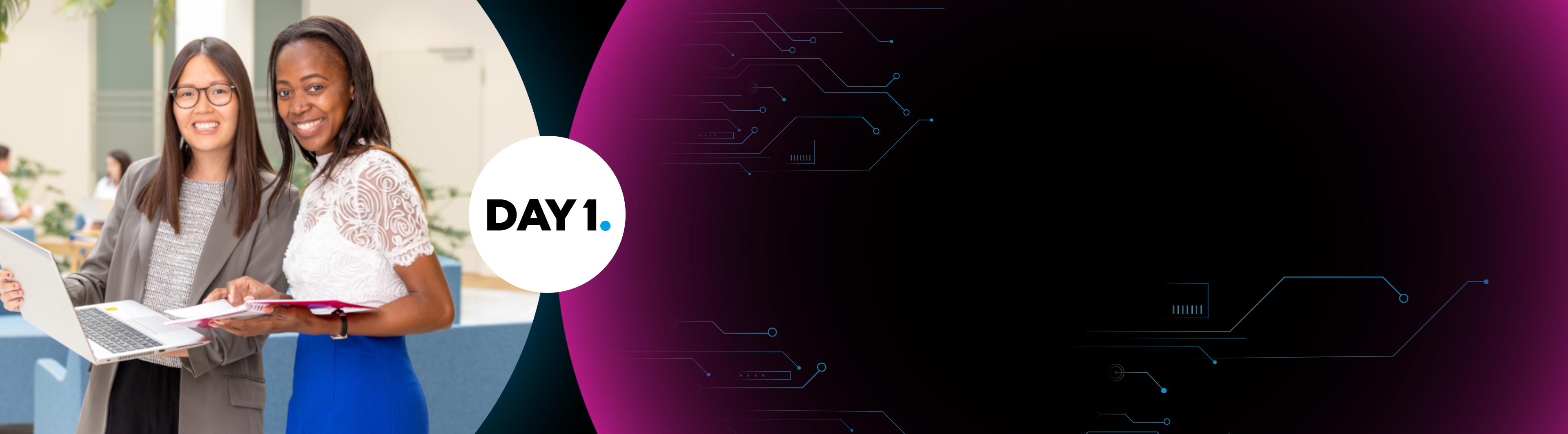
Welcome to
Germany IT Hub
As IT experts inside our manufacturing sites, we are responsible for powering our P&G business units to win through industry leading data flow and cutting-edge digital innovation. We equip our manufacturing sites with the latest IT Technology & Solutions required to run, improve and innovate processes in all areas like - Design, Engineering, Quality etc to further drive automation and digitization of our manufacturing sites.
Our experts are working on:
Business Applications used by our industrial sites (Enterprise Resource Planning like SAP, Manufacturing Execution Systems like Proficy, Product Lifecycle Management backbones)
Integration Solutions to enable a touchless data-flow across the IT (Information Technology) and OT (Operation Technology) applications used at a site
- Innovative Projects to optimize and automate processes via the leverage of OT data and AI Models that are scalable
We build data-driven platforms to enable faster innovation cycles by providing the right data at the right time, real time touchless quality assurance and reduce manufacturing expenses.
Our mission is to enable a Touchless data flow across the different components required to make, pack and ship products with quality, by leveraging the power of data for analytics and AI Models. We aim to enable a continuous exchange of data between industry partners to optimize the end-to-end the supply chain.
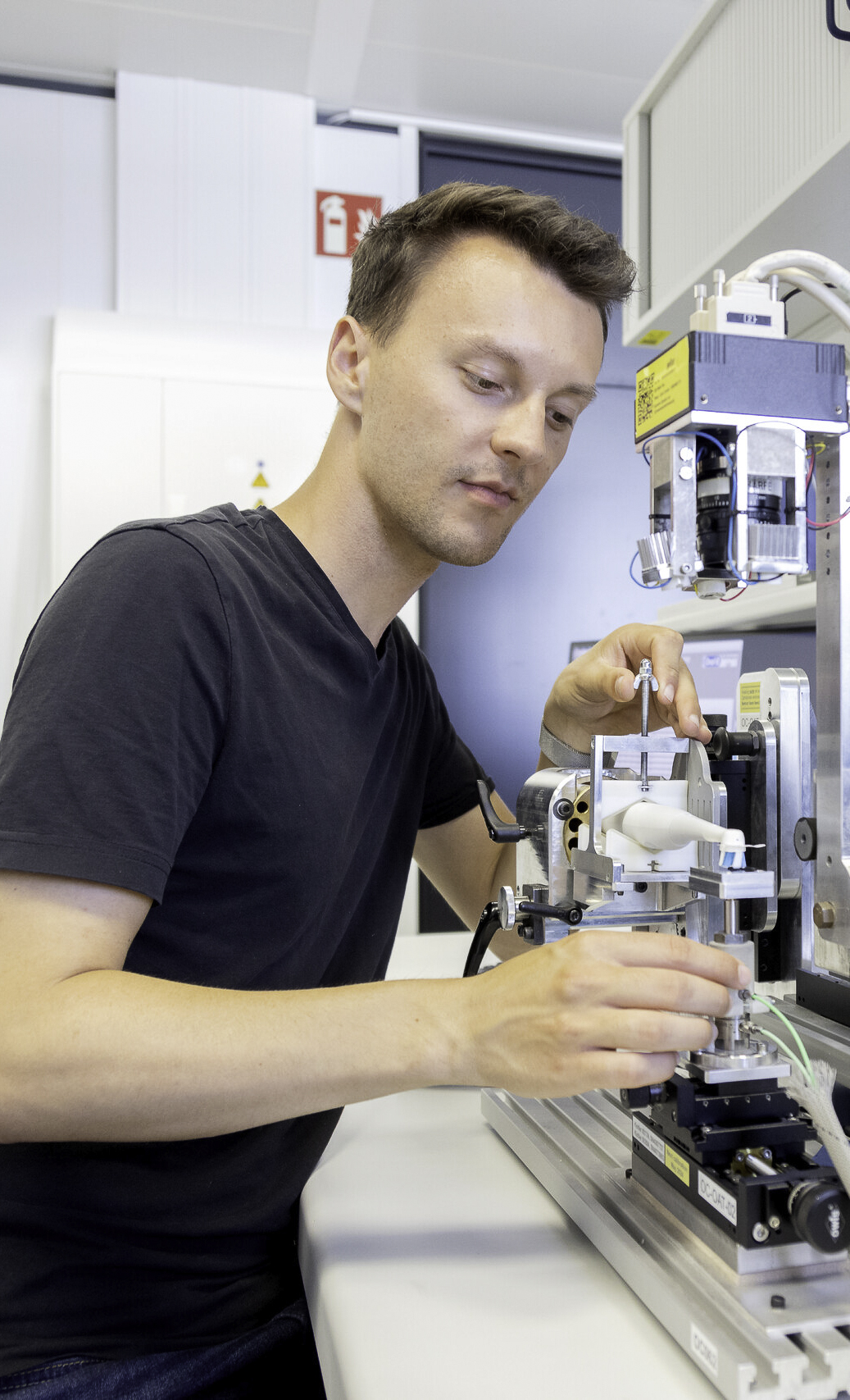
Learn more about one of our Digital products built by our IT Experts:
Problem Statement
P&G has 130 manufacturing facilities in more than 35 countries around the world, with billions of products coming out on those manufacturing lines. We have a large manufacturing footprint built over a long period, and the shop floor equipment is not the same in each of the manufacturing facilities. That lack of standardization makes it difficult to digitally transform at scale. The transformation requires taking data from equipment sensors, applying advanced analytics to derive descriptive and predictive insights, and automating corrective actions. The end-to-end process requires several steps, including data integration and algorithm development, training, and deployment. It also involves large amounts of data and near real-time processing. We need the capability of making the data compatible from those different sources so that we can work on those and replicate success. The result will be faster deployment, faster time to market, more productivity, and doing things once instead of many times.
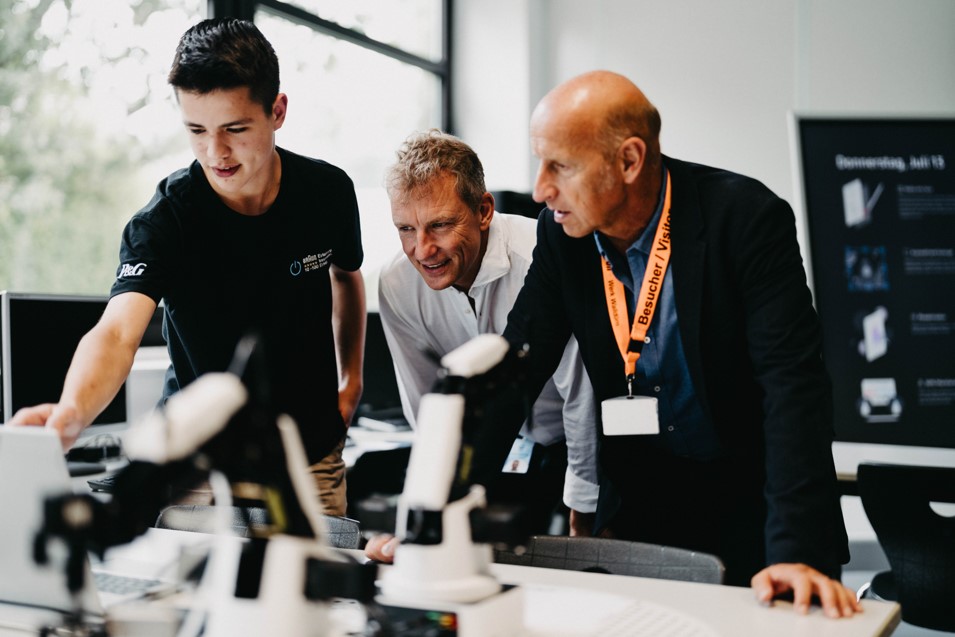
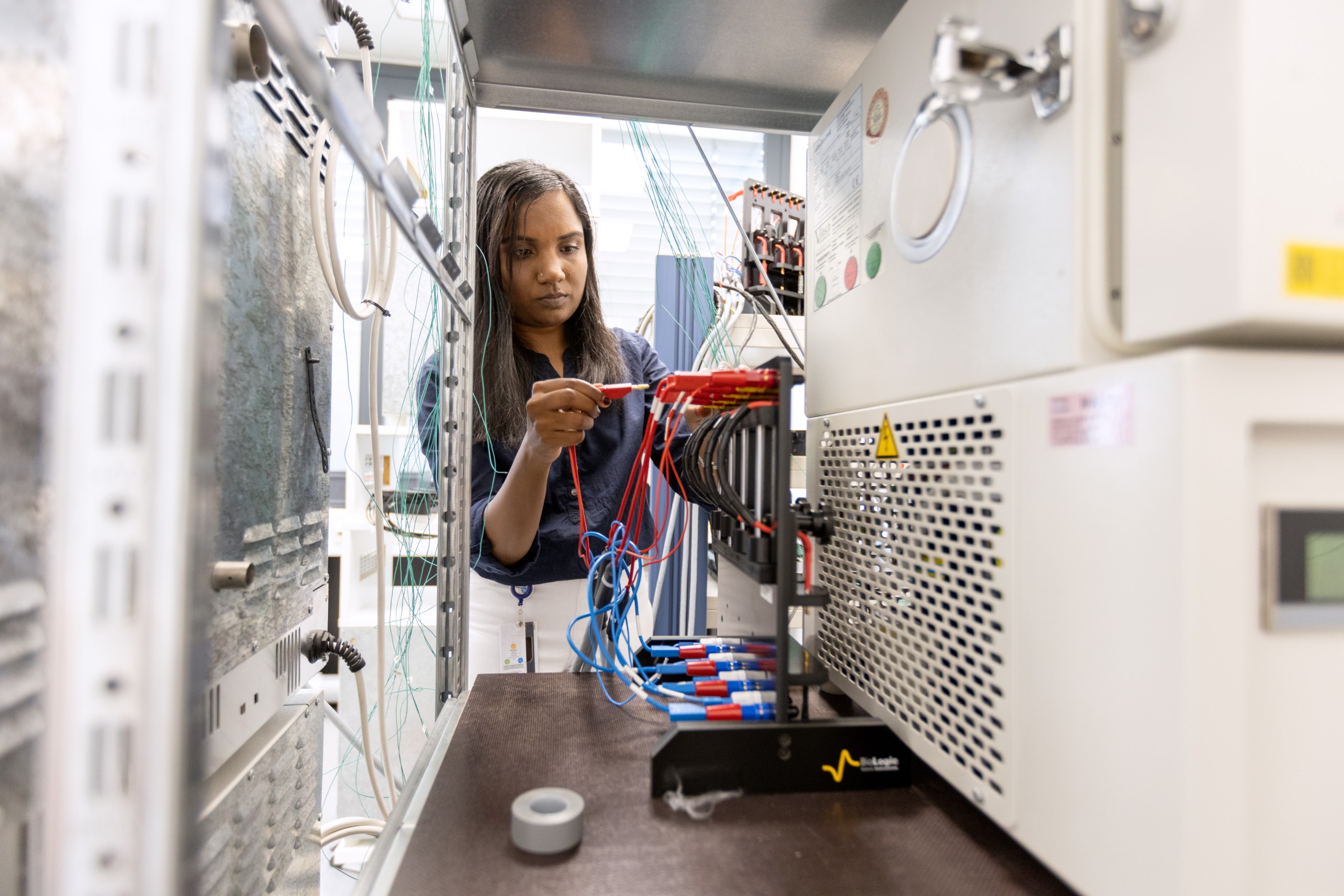
Idea/Solution
The digital transformation of P&G’s manufacturing IoT (Internet of Things) platform will enable the company to check product quality in real-time directly on the production line, maximize the resiliency of equipment while avoiding waste, and optimize the use of energy and water in manufacturing plants. For example, with the help of those algorithms, a line operator will immediately know if a machine is not cutting sheets of paper to the correct length, and they can adjust. Or for instance, the production of diapers involves assembling many layers of material at high speed with great precision to ensure optimal absorbency, leak protection, and comfort. The new IIoT (Industrial Internet of Things) platform uses machine telemetry and high-speed analytics to continuously monitor production lines to provide early detection and prevention of potential issues in the material flow. This, in turn, improves cycle time, reduces network losses, and ensures quality, all while improving operator productivity. Another use case that we replicate across many plants is using machine learning to optimize energy and water consumption, which will reduce the carbon footprint and support our 2040 carbon neutrality goal.
Strategy to Win
As part of P&G's tech modernization, we are leveraging the Microsoft Cloud to accelerate and expand P&G’s digital manufacturing platform and enhance the Industrial Internet of Things (IIoT). With Microsoft Azure serving as the foundation, it is the first time P&G will be able to digitize and integrate data from manufacturing sites around the world by using the IoT Edge and the IoT Hub. At P&G, we have so many examples of Data & AI (Artificial Intelligence), Cloud capability, DevOps, APIs, creating better business models, and enabling scalable predictive quality, predictive maintenance, controlled release, touchless operations, and manufacturing sustainability optimization.
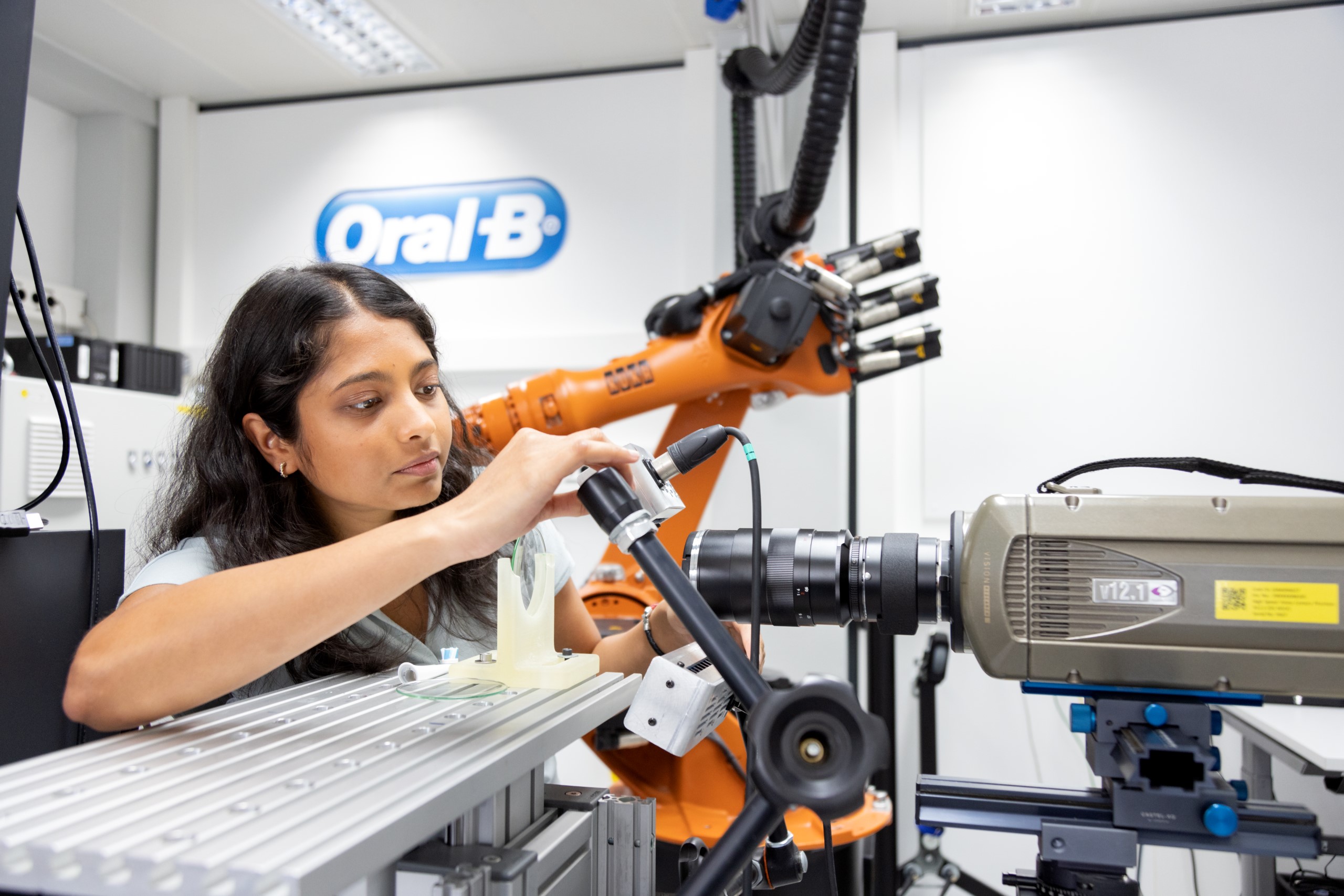